产品知识cpzs
为什么冲压模具凹模经常使用高速钢且需要深冷处理?
经常会看到日本客户给我们下单的凸模零件/冲压凹模零件采购高速钢材料,而且要求一定要进行深冷处理?
高速钢主要是用来制造冷挤压模具及冷墩压模具,特别是Mo系高速钢比W系高速钢韧性更加优越。高速钢用于模具的主要工艺难点在于热处理技术的掌握。高温淬火后需在一次硬化范围内回火三次,以获得高硬度和热硬性。主要缺点是在某些场所硬度不足。为了改善模具强韧性,近年来高速钢的传统淬火回火工艺也发生了变革。
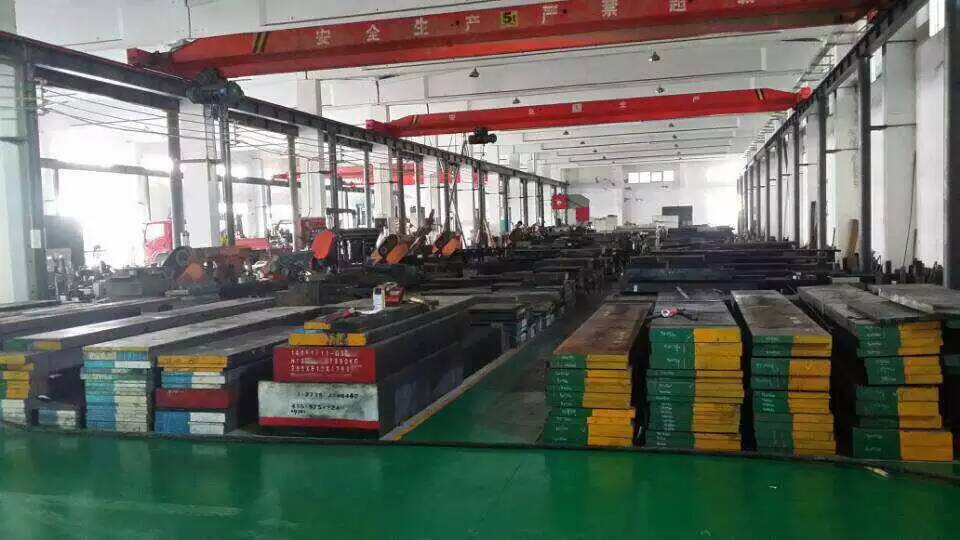
说说一些应用实例:
(1)凸模:汽车厂的高速钢凸模,未经深冷处理时只能使用10万次,而采用液氮经-196×4h深冷处理后再400回火,使用寿命提高到130万次。
(2)冲压凹模:生产使用结果表明,深冷处理后产量提高二倍多。
(3)硅钢片冷冲模:为降低模具深冷处理后的脆性和内应力,将深冷处理与中温回火相配合,可改善模具抗破坏性及其它综合性能,模具的刃磨寿命提高3倍以上,稳定在57万冲次。
高速钢的冷处理目的是将淬火钢件冷却到零下(一般为-60-70),使钢内的残余奥氏体转变为马氏体。过去工业上采用高速钢冷处理主要应用于缩短热处理生产周期,即用淬火+冷处理+一次回火来代替处理方法,即在-100 -196(液氮)处理淬火零件,其后在400回火一次,不必需原来23次的重复回火。经深冷处理后零件的硬度和耐磨性进一步改善,耐磨性可提高40%,既缩短回火时间,节省了能量,又明显提高了模具使用寿命。20世纪70年代以来,国内外对深冷处理的研究工作卓有成效,前苏联、美国、日本等国均已成功利用深冷处理提高工模具的使用寿命、工件的耐磨性及尺寸稳定性。
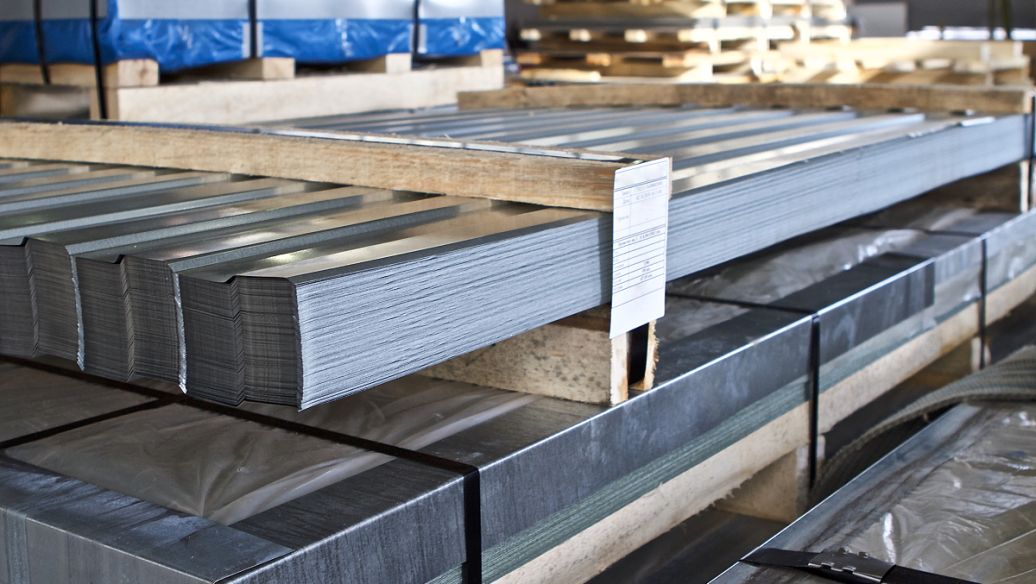
高速钢深冷处理过程中,由于残留奥氏体向马氏体以及超细碳化物的析出,硬度、耐磨性、冲击韧性、红硬性得到提高。 高速钢深冷处理的同时由于超微细碳化物颗析出,均匀分布在马氏体基体上,减弱了晶界催化作用,而基体组织的细化既减弱了杂质元素在晶界的偏聚程度,又发挥了晶界强化作用,从而改善了高速钢的性能,使硬度、冲击韧性和耐磨性都显着提高。模具硬度高,其耐磨性也就好,如硬度由60HRC提高至62-63HRC,模具耐磨性增加30%40%。
作为一种新工艺深冷处理应用在高速模具钢的热处理中,可显着提高模具的使用寿命,具有很大的实用价值。
模具钢分为国产和进口的价格区间也不同,考虑到钢材在一定时间段内的价格浮动,您可以咨询一下盈钢金属客服,得到实时钢材报价!